CNC technology column CNC machine tool new machine acceptance method Wei Xiaoning, Li Yan, Guo Tao, Li Qing, Hu Hong Machinery Industry Machine Tool Product Quality Testing Center, Xi'an 710048 Wei Xiaoning acceptance of electromechanical liquid CNC machine tools, whether it is pre-acceptance or final Acceptance is very important. The whole process of CNC machine tool acceptance involves many aspects such as management technology trade, which is a complicated process. It is directly related to the machine's functional reliability machining accuracy and comprehensive machining capabilities.
The necessity of 1 inspection The main purpose of the new machine inspection is to determine whether the machine tool meets its technical specifications and to determine whether the machine tool can accurately machine the parts according to the predetermined target. In many cases, the acceptance of new machines is determined by processing a typical typical part of the machine to determine whether the machine can pass the acceptance. But this is often not enough.
The first new machine arrives at the scene through the transportation link. Due to the vibration and deformation generated during transportation, the horizontal reference and the accuracy of the factory inspection are deviated, and must be re-adjusted.
The adjustment of the second machine tool level will have an impact on the relevant geometric accuracy items. The large and medium-sized CNC machine tools are particularly affected by this, so the geometric accuracy must also be re-examined.
The third position accuracy detection element encoder grating is directly mounted on the lead screw and the bed of the machine tool, and the geometric precision adjustment will have a fixed influence on it, so the positional accuracy of the machine tool should also be checked.
The position accuracy deviation obtained by the 4th inspection can also be adjusted directly by the error compensation software of the CNC machine tool to improve the positional accuracy of the machine tool.
Therefore, when testing the new machine tool, only the method of checking the accuracy of the test part is used to judge the overall quality of the machine tool, and as a comprehensive inspection of the position accuracy and the work accuracy, the only way to ensure the working performance of the machine tool is as soon as possible. The method and steps for producing high-quality 2 inspections are to carry out all inspection and acceptance of CNC machine tools. The workload is large and complicated, and the technical requirements for test and inspection are also very high. It is necessary to use high-precision instruments for the electromechanical and liquid parts of the machine tools. The machine performs comprehensive performance and single-item performance testing, including series tests of running stiffness and thermal deformation machine tools, and finally obtains a comprehensive evaluation of the machine tool. It can't be done for ordinary users, and it is not necessary. Our acceptance work is based on the acceptance conditions specified on the machine tool certificate and the actual detection methods provided by the user. It can be used to determine the technical indicators on the machine tool certificate. The result of the test is stored in the technical file as the original data of the machine tool, and serves as a technical indicator for future maintenance.
The following briefly introduces the acceptance work of the CNC machine.
2.1 Unpacking Inspection After the CNC machine tool arrives at the factory, the equipment management department shall promptly organize the relevant personnel to open the box for inspection. If the short-cut or model specifications are found to be inconsistent or the equipment has been subjected to collision damage, moisture and corrosion, etc., the quality of the equipment shall be seriously affected. The relevant departments shall promptly report the evidence collection or claim.
Although the unpacking inspection is an inventory check, it is also very important and cannot be ignored.
2.2 Appearance inspection The visual inspection includes the appearance of the machine tool and the visual inspection of the numerical control cabinet. The visual inspection mentioned here refers to various inspections that can be carried out without the use of the naked eye, such as whether the paint on the machine tool is peeled off, whether the protective cover is intact, and whether the work surface has scratches or scratches.
2.3 Machine tool performance and CNC function acceptance Machine tool performance inspection Machine tool performance mainly includes spindle system performance, feed system performance, automatic tool change system electrical device safety device lubrication device gas-liquid device and various auxiliary devices.
There are more than ten inspection contents of machine tool performance, and the inspection items of different types of machine tools are different. The inspection is mainly to check whether the moving parts and auxiliary devices are abnormal and noise during start-stop and operation, and to cool the system cooling system and whether the devices are normal. Check that the safety device is complete and reliable.
The best way to verify the CNC function is to program it yourself and let the machine run automatically for 16 or 32 hours under no-load conditions. In the inspection procedure, all the functions that the machine should have, as well as the various speeds of the spindle and the various feed speeds of the coordinate axes, and the automatic exchange of the table are all included.
2.4 CNC machine tool accuracy acceptance CNC machine tool accuracy acceptance, must be completely dry in the installation of the foundation, and in accordance with 13,230996 metal cutting machine tool inspection rules or related standards after installation and commissioning. Accuracy detection content mainly includes geometric accuracy position accuracy and cutting accuracy.
The geometric accuracy of the CNC machine tool for the acceptance of geometric accuracy of the machine tool is a comprehensive reflection of the key components of the machine tool and its assembly.
Commonly used detection tools are precision level instrument precision square box square ruler parallel light tube thousand micrometer spindle spindle and so on. The accuracy of the inspection tool must be higher than the measured geometric accuracy, otherwise the result of the measurement will be unreliable. The specific detection method can be referred to the relevant standards, and will not be described here. It should be noted that the detection of geometric accuracy must be completed after the fine adjustment of the machine. It is not allowed to adjust the detection items, because some items of geometric precision are related to each other, and attention should be paid to reducing the errors caused by the detection tools and detection methods.
The main testing tools are laser interferometer 360 tooth indexing standard turntable or multi-faceted prism.
The positioning accuracy of CNC machine tools can be understood as the running accuracy of the machine tool. Ordinary machine tools are manually fed. The positioning accuracy is mainly determined by the reading error. The movement of the CNC machine tool is realized by digital program instructions. The moving parts of the bed are completed under the control of the numerical control device. The moving parts can be controlled under the command of the program. The accuracy achieved directly reflects the precision that can be achieved with machined parts. Therefore, the positioning accuracy is an important test content.
The detection method of the positioning accuracy is generally performed according to the corresponding accuracy acceptance criteria. European machine tool manufacturers generally adopt the 01003441 standard; Japanese machine tool manufacturers usually use 3 23021997. It should be noted that different standards have different definitions of accuracy. It is necessary to clarify the definition and calculation method of each standard accuracy index during acceptance. .
4.210 End Instruction Day 0 The main program block is the part of the NC program. It is executed, and there may be a CNC command to execute later. Therefore, the END instruction of this system must be followed by a relay number. The relay can be an internal relay or an external relay. The state of the relay should be the whole, and the logic block starts with the PCT instruction. The end state until the end of the END instruction. When the status is 1, the block execution is completed. The system will decide whether to follow the relay ring or the end of the program return according to the state of the relay after the command.
1 main program 2.
4.3 Transmitting Instructions and Receiving Instructions The system is also equipped with a signaling command M21 and a receiving command 22 for coupling with an external programmable logic controller. Tim 21 instructions to achieve the output of the CNC host and external, 1 output. The elbow 22 command realizes the input connection of the numerical control host and the external type, 10.
5 Conclusions The programmable logic control is realized by software, and the software is integrated into the single-chip numerical control system by implementing some new software processing methods, which effectively and effectively solves the control of the input and output switching quantity in the numerical control system. Due to the use of stand-alone control, the cost of the control system is greatly reduced. The reliability of the control system is improved due to the reduced number of links. This method has been applied to the domestic economical numerical control system, and it has been proved that it can meet the needs of users.
Wang Wenxi, Li Lanji. Performance analysis of economical CNC systems. The error caused by various factors such as the 21st page and the cutting conditions can be made, so the influence of these factors should be minimized when measuring the test piece and the test piece. The main content of the machining center cutting test is the position accuracy position accuracy and the surface roughness of the machined surface. Most machine tool builders use the standard round diamond square test developed by the US National Aerospace Standard to verify cutting accuracy.
The standards for the standard CNC machine tool testing based on the test vary from country to country, and the relevant standards can be referred to during the test.
3 Conclusion In the accuracy acceptance, if the technical indicators of important projects are unqualified and affect the users, they should promptly negotiate with the machine tool manufacturers, request the repairs to report to the State Import and Export Inspection Bureau in a timely manner, and make claims through the national legal procedures. At the same time, special attention should be paid to the validity period of the claim and the quality guarantee period. Knowing these basic questions is extremely beneficial to our equipment acceptance management. Reduce unnecessary losses.
087421.21997 General rules for machine tool inspection. Determination of the positioning accuracy and repeat positioning accuracy of the CNC axis.
Ren Jiaping. Accuracy and precision are not the same. Manufacturing technology and machine tools, Wang Zhaoyuan. Several questions on the acceptance of large-scale CNC machine tools 1 Manufacturing Technology and Machine Tools, 1999.
NEST automation tips can be used for research and development and other commonly used applications with needs of high-throughput pipetting in genomics, proteomics, cytomics, immunoassays, metabolomics, biopharmaceuticals.
Features:
• Electron beam sterilization: safe and fast, without chemical residue.
• Good Air Tightness and Adaptability
The structure mapping is conducted per the original adapter and the proven injection-molding ensures that the products have good air tightness and adaptability, improving the mechanical precision of the products during work.
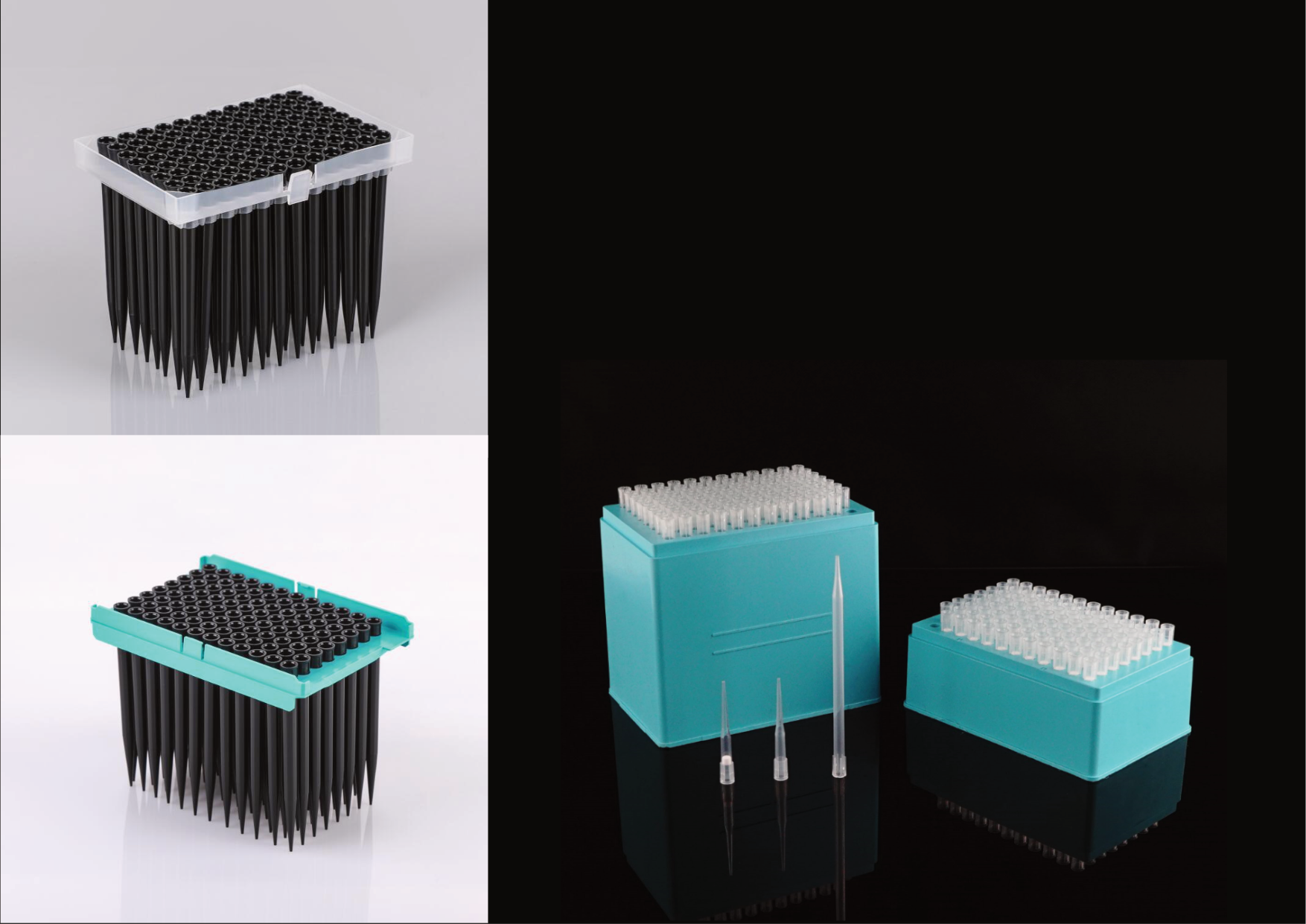
Robotic Pipette Tips,Eppendorf Micropipette,Pipet Tip,Pipette Filter;Beckman Tips;Hamilton Tips;Tecan Tips
Wuxi NEST Biotechnology Co.,Ltd , https://www.nest-biotech.com