According to the division of hazardous environments developed by the International Electrotechnical Commission (IEC), it is clearly defined that under atmospheric conditions, the environment in which dust or fibrous combustible substances and air-shaped yang mixture are ignited and burned to reach unburned mixtures is explosive. Dust environment is called Class I environment. Under atmospheric conditions, an atmosphere in which a mixture of gas, vapour or mist-like combustible material and air is ignited and burned and passed to the entire unburned mixture is an explosive gas atmosphere, known as a Class II environment.
Hazardous locations are areas in which dangerous environments occur or are expected to occur in quantities sufficient to require special measures for the structure, installation and use of electrical equipment. The hazardous locations are divided into different areas depending on the frequency and duration of the explosive environment.
(1) Division of explosive dust environmental danger zones:
According to the frequency and duration of the occurrence of combustible dust/air mixture and the thickness of the dust layer, it can be divided into 20 zones, 21 zones and 22 zones.
- Zone 20: zone 20. In the normal course of operation, combustible dust is continuously or frequently present in an amount sufficient to form a combustible dust and air mixture and/or may form an uncontrollable and extremely thick layer of dust and inside the container. The EN50281-1-1 standard specifies the structure and design of the electrical equipment housing used in Zone 20. IEC 60241-11 supplements the electrical equipment used in Zone 20, including intrinsically safe explosion protection. Zone 20 Application Category 1 (Dust) Electrical Equipment.
- Zone 21: Zone 21. During normal operation, there may be sites where the amount of dust is sufficient to form a mixture of flammable dust and air but not zone 20. This area includes sites that are directly adjacent to the point where the dust is discharged, where dust is present, and where flammable dust and air mixtures are likely to produce flammable concentrations under normal operating conditions. Mills, coal, grain warehouses, and packaging lines are surrounded by typical 21-zone locations. In Zone 21, explosive dust mixtures may occur due to dust leakage.
- Zone 22: zone 22, a site in which flammable dust clouds occasionally appear under abnormal conditions and are present only for a short period of time or where flammable dust occasionally accumulates or there may be a dust layer and produce a flammable dust air mixture. If it cannot be ensured that the flammable dust accumulation or dust layer can be excluded, the non-21 area should be divided. Zone 22 must use category 3 (dust) explosion-proof electrical equipment. If the dust in an explosive atmosphere is electrically conductive dust, Type 2 (dust) explosion-proof electrical equipment shall be used in accordance with EN50281-1-2.
(2) Division of hazardous areas of explosive gas atmospheres:
According to the frequency and duration of the occurrence of flammable gases, hazardous areas are divided into Zone 0, Zone 1 and Zone 2.
- Zone 0: Zone 0. A site where explosive gas atmospheres continuously appear or exist for a long time. The hazardous environment exists for more than 1000 hours/year.
- Zone 1 : Zone 1. During normal operation, there may be places where explosive gas atmospheres may occur. The hazardous environment exists between 10-1000 hours/year.
Zone 2: Zone 2. In normal operation, an explosive atmosphere cannot occur. If it occurs occasionally and only for a short period of time, the hazardous environment exists for less than 10 hours/year. Herein, "normal operation" refers to normal driving, running, parking, loading and unloading of flammable substances, opening and closing of closed container lids, safety valves, discharge valves, and all plant equipment operating within their design parameters.
Gas Group and Temperature Group / Explosion Protection Technology Edition
For Type II explosive gas atmospheres, the explosive gas is divided into three groups of A, B and C according to the maximum test safety gap or the minimum ignition current ratio of the explosive gas mixture. Gas grouping and ignition temperature are related to the mixed concentration of flammable gas and air under certain ambient temperature and pressure.
The temperature group is the electrical equipment used in explosive atmospheres divided by the highest surface temperature, and the highest surface temperature when the electrical equipment is operating under the most unfavorable operating conditions within the specified range, any electrical equipment that may cause the surrounding explosive atmosphere to ignite The maximum temperature reached by any surface of an electrical device or not seen. The temperature group of the explosive gas environment is divided into six groups. When the basic ambient temperature is assumed to be 40°C, the temperature of each group is
- T1--450°C,
- T2--300°C,
- T3--200°C,
- T4--135°C,
- T5--100°C,
- T6--85°C.
Here are some typical explosive gas groups and temperature groups.
For the explosive dust environment, the ignition temperature of the dust is divided into three groups of T11, T12, and T13, corresponding to the ignition temperature.
- T11--- greater than 270°C;
- T12---200°C;
- T13---150°C.
For electrical equipment whose voltage does not exceed 1.2V and whose current does not exceed 0.1A, and whose energy does not exceed 20 microjoules or whose power does not exceed 25mw, after being approved by the explosion-proof inspection department, it can be used directly in explosive gas atmospheres in factories and underground in coal mines.
Basic Principles of Explosion Protection / Explosion Protection Technology Edition
There are many types of combustibles used in industrial production, and the amount of combustibles is huge. Moreover, the production process is complicated. Therefore, various protective measures must be taken according to different conditions. From the point of view of the destructive power of the explosion, the explosion generally requires five conditions:
(1) Flammable substances (sources of release) that provide energy;
(2) Auxiliary combustion oxidizer (oxidant);
(3) Uniform mixing of flammable substances and combustion aids;
(4) The mixture is placed in a relatively closed space (surrounding body);
(5) Ignition sources with sufficient energy.
The ignition source, combustible material and combustion improver in the above conditions are the three elements of combustion explosion. Explosion protection technology is based on these explosion conditions and adopts corresponding technical measures and management measures to achieve the purpose of preventing accidents.
(1) Suppression of the concentration of combustibles
The intensity of explosion is closely related to the concentration of explosive mixture. The relationship between the explosion intensity and the change of concentration is similar to the sine curve of the cycle. If the concentration is too low or too high, no explosion occurs. These two points are called the lower explosion concentration or the upper explosion limit. concentration. Below the lower explosive concentration, the mixture cannot be ignited because the calorific value of the flammable material is so low that it cannot maintain the minimum temperature required for the flame to propagate through the mixture; if the concentration increases gradually beyond the upper explosion concentration, the combustible material Increased, but the oxygen concentration of the combustion support is lower than the stoichiometric value, it can not meet the need of complete combustion of the mixture, and it will not explode.
Therefore, the occurrence of an explosion accident can be prevented through the control of the concentration of combustibles, or the destructive power that can be caused by an explosion accident can be minimized.
(2) Control of oxygen concentration
When an inerting medium is added in an explosive atmosphere, on the one hand, the oxygen component in the explosive atmosphere can be diluted, the opportunity for the action of combustible molecules and oxygen molecules is reduced, and the combustible components are also isolated from the oxygen molecules between them. A layer that does not burn is formed; when the activated molecules collide with the inerting medium particles, the activated molecules lose the activation energy and cannot react. On the other hand, if the combustion reaction has taken place, the resulting radicals will interact with the inertizing medium particles, causing them to lose their activity, leading to interruption of the combustion chain reaction; at the same time, the inerting medium will also absorb a large amount of heat released from the combustion reaction, making The heat cannot accumulate, and the combustion reaction does not spread to other combustible components, which suppresses the combustion reaction.
Therefore, by adding an inerting medium to the combustible/air explosive atmosphere, the explosive range of the combustible component is reduced. When the inertizing medium is increased to a sufficient concentration, the upper and lower explosion limits can be coincident with each other, and then the inerting medium concentration can be increased. Combustion air mixture will no longer burn.
(3) Control of ignition source
The influence of temperature on the chemical reaction speed is particularly significant. For the general reaction, if the initial concentration is equal, the reaction speed is accelerated by approximately 2 to 4 times for every 10°C increase in temperature. Therefore, the temperature (that is, the ignition source commonly referred to) makes it possible to speed up the reaction and cause the initial factor of an explosion accident. Controlling the ignition source makes it one of the important measures to prevent explosion accidents.
(4) Weakening explosion pressure and shock wave
One of the important characteristics of the explosion phenomenon is that when explosives explode, high-temperature and high-pressure gas products swell at a very high speed, causing the pressure in the enclosure to increase rapidly, which in turn causes the enclosure to burst, forming shock waves and causing destructive forces. In order to prevent or reduce the sudden increase of the pressure in the surrounding body due to the explosion, the enclosure should be relatively closed as much as possible.
Type of explosion-proof electrical equipment / explosion-proof technology
(1) Flameproof structure: EEx d
Electric sparks and arcs can ignite explosive mixtures. The gap-proof flameproof structure established by Germany is a more reliable method of preventing arcs and other ignition of surrounding explosive mixtures. The re-explosive danger zone of the electrical equipment with explosion-proof structure is extremely widely used. It can not only prevent the explosion of fire, but also the housing can withstand a certain over-voltage. It has a sufficiently strong enclosure that withstands 1.5 times the maximum explosion pressure of the internal explosive gas mixture and must not be smaller than 3.5 x 10pa. It is ensured that no deformation or damage occurs, no permanent deformation occurs, and there is a certain structural gap so that the injected combustion products are cooled down to a temperature lower than the autoignition temperature of the external explosive mixture by a certain length of the flange. The structure gap may be composed of a plane joint surface or a cylinder joint surface, and may also be a structure composed of a curved road, a thread, or a barrier type. In addition to this. Such as micro-holes, nets, laminations, sand and other structures also belong to the explosion-proof form of this principle. Flameproof electrical equipment used underground in coal mines must be stronger.
Equipment used for Class I mining face shall be made of steel plate or cast steel. Class I equipment for non-excavating face shall have a shell with a grade not lower than that of HT25-47 gray cast iron. Class I portable equipment And type II equipment, the shell can be made of light alloy with tensile strength of not less than 117.6N/mm (12kg/mm) and magnesium content of not more than 0.5% (weight ratio).
(2) Increased safety structure: EEx e
The increased safety structure is also widely used in explosion-proof electrical equipment such as motors, transformers, lamps, and electrical equipment with inductive coils. It adopts a series of safety measures on the equipment, such as the use of high-quality insulating materials, lowering the temperature rise, increasing the electrical clearance, and improving the quality of the wire connection so that it will not generate sparks, arcs or dangerous temperatures to the maximum extent possible. Or, using an effective protective element to produce a spark, arc or temperature that does not ignite the explosive mixture to achieve explosion-proof purposes.
Another type of explosion-proof measure similar to the increased safety type is the so-called non-spark type, which is an electrical device that does not generate sparks and dangerous high temperatures during normal operation, and it cannot generate detonation faults. Compared with the safety-enhancing type, there is no provision for additional additional measures to improve the safety and reliability of the equipment. Therefore, the safety of the sparkless type is lower than that of the increased safety type, and it can only be used in the dangerous environment of Zone 2.
(3) positive pressure type structure: p
The explosion-proof principle of this structure of electrical equipment is to ensure that the pressure of the internal protective gas is higher than the surrounding to prevent the explosive mixture from entering the enclosure, or that a sufficient amount of protective gas passes through the enclosure to reduce the concentration of the internal explosive mixture below the lower explosive limit.
Under normal circumstances, there must be no dead angle inside the electrical equipment that affects safety. During normal operation, the air pressure or inflation pressure at the air outlet must not be lower than a certain value, otherwise an alarm or power cutoff will be issued immediately. Sparks and arcs inside the equipment must not be blown out from any gap or outlet. The positive pressure type structure is not related to the level of the explosive substance in use, and is often used in a device or a large-scale electrical device in which internal components are easily damaged, or an electrical device in which the self-ignition point T4 or T5 is difficult to make into other explosion-proof structures. on.
(4) sand-filled structure: q
The sand-filled structure is filled with sand or other specified powder material in the shell so that under the specified conditions of use, the arc or high temperature generated in the shell cannot ignite the surrounding explosive gas environment.
When the medium used for the granular solid (usually quartz sand) as the isolation medium, known as the sand-filled electrical equipment; and the medium used when the curing material filler (usually epoxy resin), the ignition source sealed in Inside the packing, and when the explosive mixture is isolated from the outside, it is also called a sealing type electrical device.
(5) Intrinsically Safe Structure: EEx i
The essential safety structure is only applicable to weak current loops, such as test instruments, control devices and other small electrical equipment. Irrespective of whether it is under normal circumstances or under abnormal conditions, EDM or dangerous temperature will not detonate the explosive substances. Therefore, an explosion-proof structure with higher safety, in which the surface temperature of all components on the circuit or equipment must be less than the specified To prevent ignition caused by thermal effects.
The electrical circuit of the intrinsically safe explosion-proof structure must be isolated from other circuits in order to prevent electromagnetic or electrostatic induction of the mixed wire. In particular, the external wiring of the structure must take careful measures to ensure the explosion-proof performance of electrical equipment and wiring.
(6) Explosion-proof and oil-filled structure: o The explosion-proof oil-filled structure has nothing to do with the boost level and is suitable for small-scale operation switches. The filled fluid should have high chemical stability. In order to observe the height of the oil level, the equipment should be equipped with an oil level indicator or oil level signal device.
Oil-immersed explosion-proof switches, controllers, and other equipment, due to deterioration or leakage of oil, are difficult to repair and require special attention. In addition, the equipment can no longer be used when the explosion-proof performance is impaired due to tilting or shaking of the oil surface.
(7) Explosion-proof structure of explosive dust environment
Dust explosion-proof electrical equipment is used to limit the maximum surface temperature of the enclosure and the use of "dust-tight" or "dust-proof" enclosures to limit the entry of dust to prevent the ignition of flammable dust. This kind of equipment will install live parts in a protective enclosure, which limits the entry of dust and isolates the ignition source from the dust to prevent explosions. According to the difference in the dust-proof structure of the device, the device is divided into Type A device or Type B device. According to the dustproof level of the equipment shell, the equipment is divided into 20, 21 and 22 grades, which are applicable to dust dangerous places in 20, 21 or 22 zones.
Selection of Explosion Proof Types of Electrical Equipment in Explosive Gas Environments
For explosive gas environments in different regions (Type II environment), different types of explosion-proof types need to be selected according to actual needs.
It may be easy to see in normal practical use that many explosion-proof electrical products use a variety of explosion protection methods in one product. For example, lighting devices may employ increased safety protection (housing and terminal box), flameproof protection (switch), and encapsulation type protection (ballast). This enables manufacturers to use the most suitable composite explosion protection method. One thing to note is that the order of the explosion protection methods listed on the product nameplate will often tell the user the structure of the product. If a product is identified as Ex de, it is most likely to be flameproof with increased safety components. . Another product identified as Ex ed is most likely not a flameproof enclosure (such as stainless steel or reinforced polyester glass) with a flameproof switch or component mounted therein. Both products may be suitable for use in Zone 1, but they use different explosion protection measures to achieve the same purpose. According to their own actual needs and information they have learned, they can choose to provide a product that provides a balance between cost, performance and safety.
Common explosion protection measures
1, explosion-proof / EEx "d";
2, increase safety / EEx "e";
3, intrinsically safe EEx "i";
4, positive pressure / "p";
5, filled with oil / "o";
6, sand filling / "q";
7, no spark EEx"n";
8, potting "m" and so on
Cold Chamber Die Casting
In the die casting industry, according to the difference of equipment, it can usually be divided into cold chamber die casting and Hot Chamber Die Casting. Cold chamber die casting is most used in aluminum alloy die casting. Cold chamber die casting is suitable for die casting of various non-ferrous metals, and its models are relatively complete, and the die castings of large and small parts are more suitable for production; the production operation is relatively simple, the production efficiency is high, and it is easy to automate. At present, the most used in the industry is also cold chamber die casting.
SCZY provides one-stop services such as mold development, die-casting production, product follow-up CNC machining, and product surface treatment. We have our own precision mold workshop, die-casting production workshop, and follow-up precision CNC workshop, which can ensure delivery and quality at the same time. It also provides outsourced surface treatment services, so that customers can have no worries.
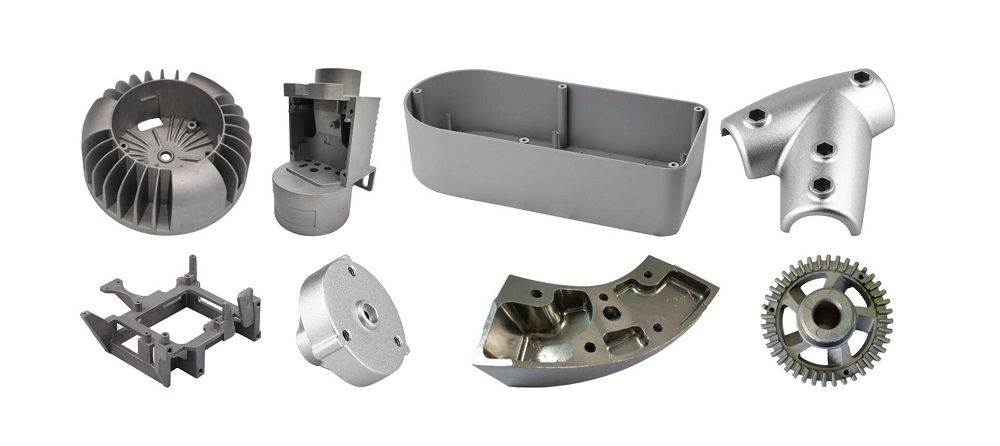